An interview with Kenny Watson, Intralogistics expert
How the modern warehouse is improving with technology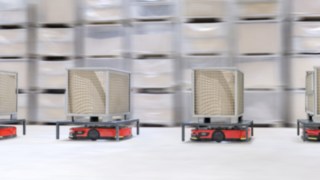
In this blog we talk to Kenny Watson, our Intralogistics expert to find out how the modern warehouse is improving with the latest materials handling technologies, to become more efficient and sustainable and how materials handling technologies can improve outcomes even in uncertain times of fluctuating demand.
How are goods protected and stored correctly in a multi-functional warehouse?
“If you look at the world of order fulfilment, particularly the online e-fulfilment centres, a lot of the technology I’m seeing is moving more towards AMR (Autonomous Mobile Robots) style ‘goods to person’ picking, where they're using these small robots to bring products to people, rather than the traditional way of people going to products. E-commence is the prime example of that. Using systems like this means there is far less risk of damage or loss to goods because there is less movement and human interaction involved.
“For example, whereas in the traditional picking model you might have five pickers each going to pick a t-shirt in a warehouse, those five t-shirts can now come to one person. This means the person doesn't do any travelling, and they're more productive (pick as a batch) as a result of the product coming to them, that's the real benefit of those type of solutions within order fulfilment warehouses.
“Another emerging technology is what's called a pouch sorter. What that means is that, whereas in the past product would be delivered to a person at a packing station, and they would put the item in a bag, seal it and put a label on, a pouch sorter does all that automatically. So, instead of it going to a person to put in a bag, it automatically drops it into a bag, seals the bag, and then automatically puts a label on the bag. Effectively you’re taking the person out the bagging process.”
Tell us about how companies are managing inventory and the digital technologies involved.
“There is a huge amount of innovation coming into the market at the moment, one of the most eye-catching being the use of drones in stock checking.
“Another solution is the use of automated trucks. Here at Linde, one of things our trucks can do is pick up a pallet with a tripod and a camera on it and drive automatically around all the locations in a warehouse taking pictures of what’s in a location, which can then be aligned to the warehouse management system and highlight any discrepancies automatically to a customer. That means the customer doesn’t need to use anyone working as stock checkers, it can all be done automatically.”
What does a good warehouse management system look like?
“A good warehouse management system needs to be configurable to suit a customer's needs – there’s no such thing as one size fits all in this industry. It also needs to be upgradable to keep up with software developments and, finally, it has to be intuitive and user friendly. Those are the things we typically look for in a warehouse management system.”
How do you fulfil customer expectations in uncertain times?
“One of the biggest challenges facing our customers right now is the lack of availability and cost of labour. Against this backdrop, what our automated solutions provide is certainty when it comes to cost and reliability in performance.
“The COVID pandemic is a prime example, with the obvious statement that automated solutions don’t catch COVID or get sick. There’s also a wide acknowledgment of the huge productivity gap between workers in our country and the rest of Europe. In short, UK businesses running warehouses need more people than their overseas competitors, which is a huge cost.
“If we look at the third-party logistics and warehouse world. A site may require 200 people, but they can only recruit 160 because of labour shortages. The view on automation is now changing from ‘I want to reduce my workforce by 40 people’ to a ‘I need automation to fulfil the workload of those 40 people that I just can’t find’.”
Is there a lot of planning involved in the materials handling process? What do operators need to know in advance before handling goods?
“First they need to understand their own profile in terms of what it is they need to fulfil, when they need to fulfil it by and how any solution that they have must be optimised to enable that fulfilment on time and in full. To achieve that optimisation they would need a partner such as Linde Material Handling to help them develop those processes and the solutions that are suitable to fulfilling those.”
Anything else you would like to add on this subject?
“I think what operators need to be thinking long and hard about future growth and the flexibility of their solutions. What do I mean by this? In traditional conveyor applications, where room for fixed assets is reducing and volume is growing, they will come to a grinding halt unless they change all the conveyors that they currently have. One of the solutions that can help in this is the introduction of smaller AMR robots that can bring the goods to the operator, because you can add more and more of those. That’s what I mean by the flexibility for growth compared to what you get with a fixed asset like a conveyor.”