Automation at ebm-papst
Efficiency Maximized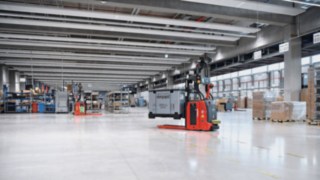
Our dispatch logistics are good, but how can we make them even better? This was the challenge facing ebm-papst, a leading producer of fan and motor products, at its site in Mulfingen, Germany. The answer: Fully automate one of its material flow processes using trusted expertise from Linde. The project has proven a huge success, so much so that transport volumes have exceeded expectations and further automation projects are already being planned thanks to this impressive start.
“A natural flow is inherently efficient,” declares ventilation and drive technology expert, ebm-papst in one of its striking promotional videos. And if you think about it, this statement makes complete sense, even to those of us not blessed with a degree in physics. After all, a flow of air never makes a detour of its own accord, does it? Rather, as is beautifully exemplified by the over 20,000 products supplied by this world leading manufacturer, it can be deliberately redirected for our benefit – to keep overloaded servers cool; to extract unwanted odors from our kitchens; to keep food on the supermarket shelves cool; or to keep our buildings well ventilated. To a certain extent, this same logic can also be applied to intralogistics. A forklift truck operator can transport pallets directly from the packing line to the handover point 30 meters away, umpteen times a day, five days a week. In itself, the process is efficient, but could it be made even better?
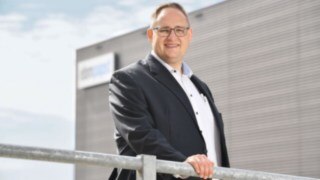
Tobias Arndt, Logistics Director at ebm-papst in Mulfingen
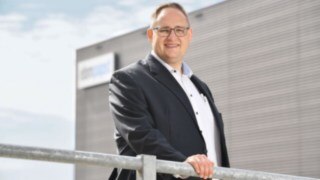
Tobias Arndt, Logistics Director at ebm-papst in Mulfingen
“Soon after we opened our new dispatch center in Mulfingen-Hollenbach in 2017, we started to ask ourselves exactly this question,” remembers Tobias Arndt, Logistics Director at ebm-papst. After all, the same process was being repeated time and time again. The family-owned company had been using automated solutions for highly standardized processes in its production facilities and high rack warehouse for some time. “So it seemed obvious to implement something similar for our dispatch logistics,” Tobias continues. “Ultimately, it makes more sense to deploy our frankly overqualified forklift truck operators in another area of the company, to tasks where they can provide more value.” You don’t need a degree in economics to understand the logic behind that.
A One-Stop Solution
Linde network partner Hofmann Fördertechnik had previously impressed with its equipment for production halls, narrow aisle warehouses, and dispatch, so when it came to finding the right automation solution, ebm-papst once again turned to this trusted supplier. When asked about his initial requirements, Tobias Arndt explains: “A static conveyor solution wasn’t an option for us because we didn’t want to divide up the gangway through the hall.” There is a lot of activity in the area around packing line 4 and the two handover points; forklift truck operators and pedestrians use the route all the time during the company’s three-shift operations. “We also didn’t want to take on major alterations such as laying rails,” he continues. “The customer had a pretty clear idea what they didn’t want,” smiles Alessandro Zuccala, Head of Intralogistics at Hofmann, who oversaw the ebm-papst project.
The first step was to analyze the facts and figures based on the key target parameters such as the required hourly transport volumes. Alessandro and his team then moved to the proof of concept stage, where they tested their proposed solution – Linde’s automated L-MATIC pallet stacker – for several days at the Mulfingen site.
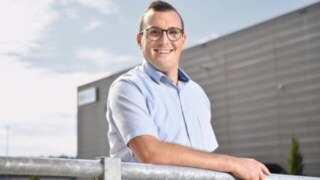
Markus Zink, Project Manager at ebm-papst in Mulfingen
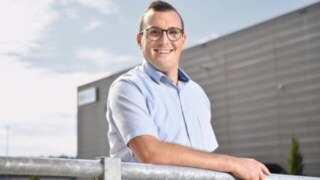
Markus Zink, Project Manager at ebm-papst in Mulfingen
“That stage was really important for us,” explains Markus Zink, the project manager for ebm-papst. “In meant we could see the idea in operation in our own dispatch center, not just on paper or at other companies.” To avoid the need for equipment such as reflectors, the application engineers from Hofmann created a digital map of the warehouse, so that the Linde L-MATICs could navigate using fixed points. This solution is also practical, since the driving routes can be easily altered at a later date should operating requirements change. The proof of concept stage also included test runs with the more than 20 different load carriers in use on packing line 4. “Some fans and motors are transported from the packing line to the handover point for the high rack warehouse; others need to go to the handover point for direct dispatch,” explains project manager Markus Zink. “Clearly our solution needed to cater for both use cases,” continues Alessandro Zuccala. To achieve this, Hofmann-Fördertechnik took on the complex task of programming the automated Linde L-MATIC pallet stackers with all the necessary process data. This included connecting the Linde trucks to the internal SAP Extended Warehouse Management (EWM) system on the ebm-papst company network. Markus Zink has been really impressed: “It was fantastic how our Linde network partner just took care of everything – the planning, the trucks, and the software requirements.”
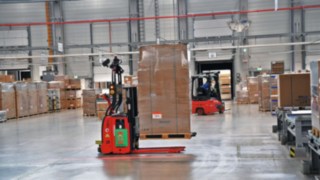
Seamless Integration
Three Linde L-MATICs have been in operation at ebm-papst since March 2020. Over and over, these highly efficient trucks remove pallets from the conveyor and transport them to the required handover point, with no human involvement whatsoever. “Our SAP EWM system sends the trucks instructions before the packages have even reached the end of the conveyor, which means the trucks can get into position in good time,” explains project manager Markus Zink. Whenever they are on the move, the trucks shine a clear red LED warning line on either side of them. They are also fitted with Linde TruckSpot™ which projects a large warning triangle onto the hall floor when they are reversing. Markus Zink is keen to emphasize the importance of these features: “Safety had to be our top priority because the trucks operate alongside other pedestrians and forklift truck operators.” For the same reason, the Linde L-MATICs are also connected to a separate combox, which, in the event of a fire in the hall, will send a signal directly to the trucks and bring them to a standstill in a position where they are not blocking any escape routes or hampering the efforts of the emergency services.
As well as working seamlessly with their human colleagues, the L-MATICs also come with a straightforward charging solution for their lithium titanate oxide (LTO) batteries. As Markus Zink explains: “Hofmann installed a new charging station with movable contacts, which the Linde L-MATICs can dock into automatically, for instance in the breaks between shifts. This means the three trucks can easily cover all our shifts even at peak times.” Plus, if a truck breaks down, “our team are ready and waiting to help,” confirms Alessandro Zuccala from Hofmann. His specialist team can conduct remote maintenance work on the trucks, meaning they can easily assist with software problems without the need to call in external experts. For ebm-papst’s Logistics Director Tobias Arndt, “that’s a real plus.” Another is that the L-MATICs are far exceeding the originally requested capacity of 36 transport runs per hour, achieving 50 runs an hour at peak times and almost 100% availability. In the words of Tobias himself: “Now that’s what I call efficient!”
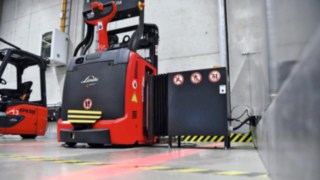
ebm-papst Mulfingen GmbH & Co. KG
ebm-papst Mulfingen GmbH & Co. KG was founded in 1963 and has since become the world’s leading manufacturer of fan and motor products. The family company operates 29 production sites and 48 sales locations around the world, providing customers from a host of different industries with bespoke, energy-efficient solutions, which range from compact, axial, and centrifugal fans to blowers, pumps, and complete drive systems. When it comes to the logistics at its main site in Mulfingen, ebm-papst relies on the technology and expertise of Linde Material Handling and its network partner Hofmann Fördertechnik. Following the resounding success of their 2018/2019 automation project, the company is now planning to automate many other transport operations at its Mulfingen site and also look for opportunities to build on these experiences at its other German sites in Landshut and St. Georgen.