Li-ION technology from Linde
The energy system for the intralogistics of today and tomorrow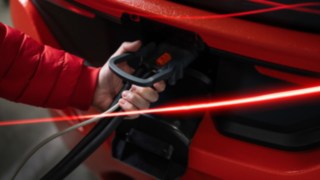
Maximum uptime and flexibility
Increasing cost pressure, tight timelines and unpredictable order peaks: the dynamics of the logistics business are changing the requirements placed on warehouse equipment and forklifts. Above all, they must be constantly available and flexible in their use. At the same time, safety and cost-effectiveness are important factors. This means that energy systems are also put to the test.
At present, it is not only in the automotive world that there are signs of a change to electromobility. The material handling equipment industry has long been a pioneer in this field. For some time now, there has been increasing demand for electric forklifts instead of IC engine-powered trucks. The challenge: to ensure the same high vehicle availability as with trucks powered by internal combustion engines. This is where Li-ION technology comes into play. It has proven its worth in everyday use – in smartphones, for example – and offers a whole series of advantages over lead-acid batteries in forklifts:



The ideal solution for every application
The use of Li-ION batteries is suitable for all applications. However, their advantages are particularly useful in intensive applications such as multi-shift operation and refrigerated storage.
Due to the elimination of emissions and possible impurities in lead-acid batteries, the technology is also particularly suitable for use in areas where a high degree of sensitivity is required, for instance the pharmaceutical or food industry.
For companies looking for an alternative to their internal combustion forklift fleet, Li-ION batteries are an environmentally friendly option.
Advantages of Linde's Li-ION solution

Linde Li-ION batteries for forklift trucks and warehouse equipment improve operation and handling. They increase truck availability and make operation more economical, safer and more sustainable. Many users appreciate the practical advantages in everyday work.
Cost-effectiveness
Li-ION batteries increase the efficiency of the fleet in operation. This is due to the technological advantages of this energy system, which offers numerous time and cost advantages in day-to-day logistics and for the associated infrastructure:
High system efficiency
The Li-ION solution from Linde has a particularly high system efficiency. The combination of Linde lithium-ion battery and Linde charger increases the energy yield by 30 percent compared to lead-acid batteries. which leads to lower energy costs.
Intelligent battery management
In addition, truck control and battery management are optimally aligned, for example through the CAN bus interface, which enables systems to communicate with each other. The battery system therefore balances peak loads, while simultaneously providing sufficient energy. This protects the battery and prolongs its operating life.
Reduced maintenance and handling costs
Conventional lead-acid batteries incur a whole host of maintenance and handling costs, which are completely eliminated with lithium-ion batteries. These include, for example, the cost of a second battery, personnel costs for replenishing the batteries with water and battery replacement.
Lean charging infrastructure
In addition, there is no longer any need for complex charging infrastructure with a separate battery room and gas suction device. The charger for the lithium-ion batteries, on the other hand, can be flexibly set up at sensible waypoints. For example, a short recharge can take place close to break areas, or in the immediate vicinity of the application area to save driving time.
Availability
To ensure smooth and efficient logistics operations, warehouse handling equipment and forklifts must be available at all times. This is one of the main strengths of Linde’s Li-ION batteries. Unlike lead-acid batteries, the technology is highly efficient and flexible in terms of charging cycles and frequencies.
High-speed charging
Linde batteries can complete a full charge cycle within just an hour. Depending on the intensity of the operation, an interim recharge during the lunch break means trucks are ready to go for several more hours.
Short interim charging preferred
With conventional batteries, it is recommended to only ever start full charging cycles in order to protect the batteries. With lithium-ion batteries, the situation is completely different: even an extremely short interim charge of just a few minutes is not only allowed, but even preferred. Their ideal state of charge is about 20 to 80 percent of the total capacity. The flexibility of the charging process significantly increases the overall availability of trucks.
Customised protection against deep discharge
Linde’s CAN bus technology allows individual settings to be adjusted for protection against deep discharge. When approaching the minimum residual capacity, the battery management of Li-ION batteries reduces the power of drive and lift functions. This value can be set individually to achieve the desired balance between truck availability and battery protection.
Different capacities for different applications
Linde offers two different capacities for each type of battery. This enables companies to design the energy supply in accordance with the operating intensity of each individual truck. For example, it is possible to use a forklift truck with a large battery to span a three-shift operation, without any need to charge the truck during this time.
Safety
Linde’s Li-ION technology also offers the highest level of operator and truck safety. Linde engineers have developed a comprehensive safety concept for the entire system, consisting of battery and truck. During the development phase, the batteries undergo a programme of special stress and crash tests.
No hazardous gases
While the hydrogen produced by lead-acid batteries can turn into dangerous oxyhydrogen gas, lithium-ion batteries eliminate this risk. In addition, the absence of the battery replacement required for lead-acid batteries means that operators are not exposed to any risk of injury. Since the Li-ION cells are virtually maintenance-free, the operators cannot come into contact with dangerous acids.
Crash-tested compartment
In accidents involving forklift trucks, enormous forces are exerted due to the weight. To ensure that the Li-ION batteries in the vehicles are protected even in extreme situations, they have been subjected to a crash test of the maximum load. In the video: thanks to its 25 mm-thick steel housing, the battery prevents the penetration of a fork even at high speed. The mechanical design of the battery therefore also meets Linde's high quality standards.
Multi-level safety system
The multi-level safety system in place with Linde Li-ION batteries applies at cell, module and battery level. In addition, battery management ensures optimum battery usage by constantly monitoring and coordinating vehicle functions, charging processes and the battery system. This prevents damage caused by overpressure, overheating, over-charging or deep discharge.
Furthermore, not only are the vehicle and battery CE-compliant, but also the entire system – consisting of vehicle, battery and charger – carries the CE seal of approval for tested safety. As a rule, this is not guaranteed when purchasing the battery as a stand-alone component.
Sustainability
State-of-the-art energy systems are not only highly efficient, but they also protect both people and the environment. Linde’s Li-ION batteries meet all sustainability requirements. For example, their operation is completely emission-free.
In addition, operating forklift trucks and warehouse handling equipment with this technology is significantly more energy-efficient, which means that less energy is consumed to achieve the same overall output.
Extended life cycle
The production of lithium-ion batteries also produces fewer pollutants than that of conventional lead-acid batteries. Another advantage of this technology is the longer life cycle of the batteries, which also helps to conserve environmental resources.
Comprehensive battery recycling
Lithium-ion batteries are the drive technology of the future. Increasing demand raises the question of how to handle this resource in a sustainable way. Despite their long service life, also Li-ION batteries eventually reach the limits of their performance. At Linde Material Handling, sustainability begins with the production of the batteries and continues at the end of their life cycle. Specialist recycling plays a crucial role in recovering valuable metals and raw materials and transferring them to a closed cycle.
Li-Cycle is certified according to ISO 14001 (Environmental Management Systems) and ISO 45001 (Occupational Health and Safety Management System).
In cooperation with Li-Cycle, Linde has developed a comprehensive recycling process. This process is capable of safely recycling almost all lithium batteries, regardless of shape, size or chemical composition. Damaged batteries can also be recycled. Li-Cycle uses an energy-saving, liquid-based process to recover valuable materials from the battery cells. Up to 95 percent of the metals can be recovered and used to manufacture new batteries.
In comparison to the extraction and processing of the raw materials, the recycling process reduces emissions – per metric ton of battery material – by 67 percent for CO₂, 86 percent for sulphur oxides, and 89 percent for nitrogen oxides. In addition, water consumption is reduced by 97 percent. This will further optimise the eco-balance of the already environmentally friendly batteries.
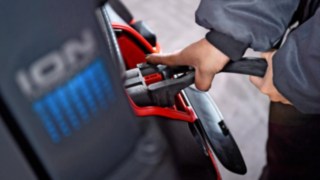
Free recycling for all Linde Li-ION batteries
Li-ION batteries purchased via Linde Material Handling can be recycled free of charge within the scope of the disposal contract. The batteries can be returned to all service partners in the Linde network or sent directly to Li-Cycle. This requires certain information, which you can find on the battery label. After you have sent the data, our logistics partner will contact you directly and take care of transporting the batteries.