Lithium-Ion technology at freight forwarder Fritz
Between charges: opportunity charging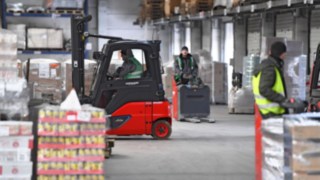
More flexible, cost-effective and robust: In the highly frequented general cargo warehouse in Heilbronn, the freight forwarder has switched its industrial trucks from lead-acid battery operation to modern Linde lithium-ion technology.
If you take a bird's eye view, the activity at the Fritz GmbH & Co. KG site has a bit of a beehive feel to it: a truck rolls into the yard every few minutes, then it’s gate up, roller shutter open, goods loaded or unloaded; the truck leaves and it's onto the next truck. At peak times here in Heilbronn, close to the Weinsberg motorway interchange where the A6 and A81 meet, around 140 trucks are handled on a daily basis. That corresponds to around 2500 consignments coming in and going out of the highly frequented logistics hub every 24 hours. The comparison with a beehive is also fitting in terms of the levels of organisation: the logistical operations in the general cargo warehouse are adjusted to the high frequency and programmed accordingly. One particular challenge here is the absence of exact timescales to indicate when goods may be delivered or collected.
This requires a great deal of flexibility from the freight forwarding staff. “Our business is fundamentally subject to extreme fluctuations,” explains Christian Czemmel, General Cargo Transport Division Leader at Fritz. Added to this is the huge variety of goods handled. “To put it simply, everything that is too big for the postal service comes in and goes out of our company – that ranges from pallet goods like personal care products, building materials or furniture all the way through to lattice boxes with machine parts and pieces of turf that the end client has ordered online.” The result of this? Both the quantity and the frequency of the goods handled change according to the time of year and the economic situation. For the pallet trucks and electric counterbalanced forklift trucks used by the operators at the site, that means on-demand deployment in many cases, as well as constantly being on stand-by. A logistics profile made for the modern lithium-ion battery solution from Linde Material Handling.

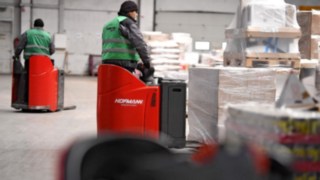
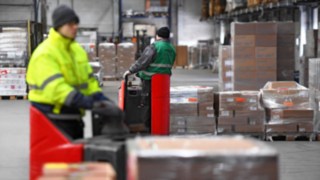
How is it better?
“Until about a year and a half ago, our forklifts were exclusively equipped with lead-acid batteries. Then a fleet renewal was due for 18 fork trucks in the cold store. We sat down with the Hofmann Fördertechnik sales consultants and looked for optimisation potential,” explains Christian Czemmel. Fellow colleague Heiko Weißert, who has worked at Fritz GmbH & Co. KG for almost 20 years as Key Account Manager with the Linde network partner, adds, “The low temperatures in the unheated hall put a noticeable strain on lead-acid batteries, particularly in winter. In tough three-shift operations, this kept hampering battery performance, resulting in trucks having to visit the changing station earlier than usual.”
That’s when lithium ion was mentioned as a low-temperature resistant alternative. “In the end, our cost-effective calculations clearly pointed towards lithium ion. At the same time, we knew which combination of truck, battery and charging device was best suited for use here.”
Valuable time used wisely
But what are the criteria that set Fritz on the path of this innovative type of energy storage? The pace at which employees work is largely dependent on incoming and outgoing trucks. When a truck arrives at one of the 44 gates, the first step involves unloading the freight at the ramp using one of the ten platform trucks and then lining it up in the hall. An employee scans the barcodes with the scanner, which then displays the corresponding storage areas. After the goods are checked in and marked, the reins are handed over to colleagues with Linde E16 counterbalanced forklift trucks, which transport heavy goods weighing up to 1.6 tonnes to the designated positions in the hall. Once the collection truck rolls into the yard – and this usually happens on the same day – the E16 is also used for loading the trailers. Over the course of the process, there are always short intervals during which the forklift trucks are stationary. There are also regular breaks. This downtime can be put to good use: for short, effective stops to charge lithium-ion batteries.
Perfectly adapted
The charging devices are strategically placed at the top of the hall – lined up for the warehouse handling equipment on one side, and for the forklift trucks, of which there are 10 in total, on the other. “The sticking point for us was the network performance. We upgraded this together with our energy supplier,” says Christian Czemmel. “For the changeover to lithium-ion technology to be as smooth as possible, it was important that we knew all about the internal processes in order to determine the required network performance and the distribution of energy demand throughout the day,” Heiko Weißert elaborates.
Successful model(s)
After 12 months of working with the lithium-ion fleet, the assessment in the Fritz general cargo warehouse is overwhelmingly positive. The devices run reliably, have sufficient power and are also cost-effective. Lastly, the lithium-ion devices are up to 30% more energy efficient than lead-acid batteries and at the same time conserve valuable (personnel) resources: “We always needed an extra worker to change the batteries in the lead-acid trucks, not to mention that we always had to keep fully charged batteries close by and that we needed a dedicated space for changing them. And because the new rechargeable batteries, unlike their lead-acid counterparts, are not only low-temperature resistant, but also completely maintenance-free, we are economising on this point as well – in the past, this necessitated an additional 90 minutes of work per day. All of that adds up!” No wonder then, that those in charge at the logistics expert are considering a company-wide switch to lithium-ion technology. “Who can say that we’re not open to new ideas in the SME sector?” laughs Christian Czemmel.
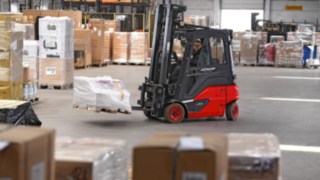
Fritz GmbH & Co. KG
Fritz GmbH & Co. KG, established in 1938 and with its headquarters in Heilbronn, is now under third-generation management. The family-run company employs a total of 672 staff, 103 of whom work in the general cargo warehouse in Heilbronn. There are 18 Linde lithium-ion trucks in operation: eight E16 lithium-ion forklift trucks and 10 T20 SP lithium-ion pallet trucks. All trucks are equipped with the Linde Safety System BlueSpot; Fritz also uses the Linde Fleet Management System connect:, for access control, among other things. All trucks operate on a full service contract hire agreement in collaboration with the servicing dealer Hofmann Fördertechnik . Work is carried out in multiple shifts, non-stop from 1:00 a.m. on Monday morning through to 7:00 a.m. on Saturday morning.